Doc. 3 TURBO WASH Strong Cleaning (Patent No. 6421093)
Strong bubble cleaning – Patent Technology Developed by Viscon (Japan) Corp.

Until now, viscosity controllers have had a two-stage configuration : a viscosity controller machine box and a solvent tank placed on top of it. In 2015, Viscon (Japan) Corp. developed and launched a three-stage viscosity controller called Viscosity controller Machine Box + Solvent Tank + Automatic Cleaning Function ( TURBO WASH ). As a pioneer of viscosity controllers, we have innovated in the market.
About 50% of the failure causes of conventional viscosity controllers
are due to the fact that a lack of cleaning has occurred to
the viscosity controller as a result.
In Japanese gravure printing plants, the length of gravure printing orders
is extremely short, compared to foreign countries.
My conversation with the President of overseas gravure printing company
President of Gravure printing company
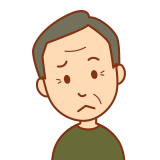
” Recently, the order lot of gravure printing
has shortened, and I am in trouble. ”
Mr. Matsuoka
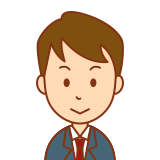
” The order is shortened ? How long ? ”
President
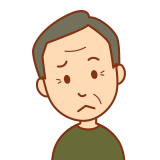
10,000 meters or 20,000 meters or so.
Mr. Matsuoka
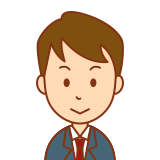
” President ! If it is long like this, and
if it is a Japanese gravure printing company,
it is not said that the print order is short,
but rather a long and good order.
in Japan. ’’
” There are 4,000 meters order in Japan,
and in the last 7-8 years, there have been 2,000 meters. ”
When I told the president of that overseas gravure printing company,
the eyes on the president’s face were pointing
and he looked very surprised.
It is not uncommon in Japan to have a company that does
6 or 7 times of changeover job per day’s gravure printing work.
A Japanese gravure printing company is doing changeover job
as 45-minutes target for one time of changeover job. ”
I continued to explain to the president,
The president was at a loss for words.
In Japan and overseas, there is a significant difference
in the speed of work setup time (preparation )
as well as differences in the quality of gravure printing.
There are various differences between Japanese and
overseas gravure printing companies.
But the failure/breakdown problem of the conventional viscosity controller
” the cleaning of the viscosity controller is insufficient as a result,
and the ink route of the pump and hose of the viscosity controller
is clogged due to the lack of cleaning as a result,
and the viscosity controller failure/breakdown is exactly
the same in Japan and overseas. ”
As a result, insufficient cleaning problems accounted for
about 50% of the failure/breakdown causes of conventional
viscosity controllers.
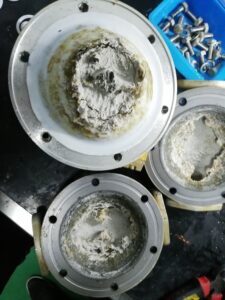
insufficient cleaning, and then failure breakdown of diaphragm pump of viscosity controller
It is by no way “deliberately” cut back on cleaning the viscosity controller.
The interest and responsibility of the operators of gravure printing
companies is to print beautifully without printing spoilage,
not to take cake of viscosity controller which exists to each
gravure printing unit.
From the operator’s point of view,
they print the gravure printing beautifully every day, and every day,
and deliver it to clients who need printed materials.
I think they are focusing on this.
For the viscosity controller next to the gravure printing unit,
I want it to be a machine that takes as little time as possible.
I always thought that this was the real intention of operators
at the gravure printing plant overseas where I visited.
As a manufacturer that manufactures viscosity controllers
and lets customers use them properly,
it is also difficult to see viscosity controllers that are not properly
used in the customers factory due to many breakdowns.
When I worked for my previous working company,
I felt a lot of hard work on the job when I went abroad.
In the meanness, due to the great
efforts of overseas customers, the viscosity controller is used properly,
and the numbers displayed on display counter of viscosity controller
are also displayed with appropriate, accurate and stable numbers.
When I met such a good viscosity controller using at overseas customers,
I was honestly happy.
( Viscon viscosity controller that is operating properly at overseas customers’ factories.
I took a picture with customers’ permission.)
Customers need a viscosity controller that doesn’t break down
and doesn’t require a lot of effort.
For that reason, about half of viscosity controller
failures/breakdown account for 50% failure due to cleaning shortages.
it is the responsibility of the true viscosity controller manufacturer
to present a solution for this 50% failure/breakdown from the machine side
of the viscosity controller,
instead of relying on the “great efforts of the customers”,
Viscon Japan’s patented technology was born from this idea and purpose,
and provides a powerful bubble cleaning method ” TURBO WASH ”.
To explain the solvent circulation cleaning of the conventional cleaning method
and the cleaning method provided by Viscon, strong bubble cleaning,
using an example,
Circulating cleaning with conventional solvents : ” Mouth wash “
Viscon Strong Bubble cleaning TURBO WASH : ” Brush teeth “
We also brush our teeth with a toothbrush every day in our daily lives.
I don’t think there are usually people who don’t brush their teeth
and live every day with just “Mouth wash”.
I think that it is because we know from experience that
“Mouth wash ” alone cannot brush teeth cleanly.
The same can be said for TURBO WASH
(Brush teeth) of powerful bubble cleaning and solvent circulation cleaning (Mouth wash)
Turbo WASH, a powerful bubble cleaning, mixes high-pressure
air in a circulating solvent for 5 seconds,
and then does not mix high-pressure air for 5 seconds continuously
for 5 minutes.
The high-pressure air mixed in the circulating solvent every 5 seconds
becomes a myriad of small bubbles, and it is brushed into the hose
or the uneven inside of diaphragm pump as a group to repeat the circulation.
Watch the YouTube Viscon video below to get a good look.
Countless small small bubbles (bubbles)
are grouped in the hose, brushing the inside of the hose and
uneven inside of diaphragm pump.
Brushing effect of TURBO WASH
Experience the ” brushing effect” with this powerful bubble cleaning
“TURBO WASH” , Viscon Japan cleaning method.
It is a cleaning ability that cannot be obtained by other cleaning methods
of conventional viscosity controller until now.
Reference:
Please refer to the following for the results of cleaning capability tests
of three cleaning methods.
👉 👉 Viscosity Controller 3 Types of Cleaning Methods Test Results
Double cleaning capacity
and
reduce cleaning effort by half.
About 50% of the causes of failure of conventional viscosity controllers
are solved by “TURBO WASH”, an optimal cleaning method for viscosity controllers developed by Viscon (Japan) Corp. who is familiar with the principle of viscosity controllers.
It has been 7 years since Viscon Japan developed and sold it.
Our customers have also appreciated the patented technology,
which is ” worth more than the price “.
👉 👉 Viscon development technology is an official patent in Japan
for viscosity controller. “TURBO WASH” patent certificate.
Click on the link below. YouTube Viscon video with the source.
Open TURBO WASH Powerful Bubble Wash PDF on a separate page.
👉 👉 TURBO WASH Strong Bubble Wash
TURBO WASH is a YouTube Viscon video of powerful bubble cleaning.
👉 👉 YouTube Viscon Video TURBO WASH
If any questions or unclear things,
please do not hesitate to contact us Viscon Japan Corporation. 👇 👇
コメント